An Oklahoma oil refinery was in urgent need of a solution to a critical exchanger that was experiencing very high process side temperatures. Scale accumulation on the cooling water side (tube side) of this exchanger was determined to be the cause of the escalation in process side (shell side) temperature. This exchanger could not be taken off-line without shutting down the process. With shutdown not being an option, a continuous injection of RYDLYME was proposed to get the refinery back to acceptable operating temperatures.
RYDLYME approach
- 440 gallons injected and pumped through at 4 gpm (once-through, online application).
RYDLYME results
- Process side temperature decreased from 300°F to 150°F; tube side decreased from 160°F to 125°F!
- Client stated that RYDLYME “worked like a champ and was shockingly good.” He was also amazed at how much of an adverse affect scale can have these units and how they operate.
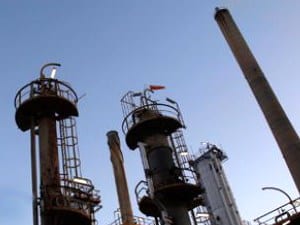